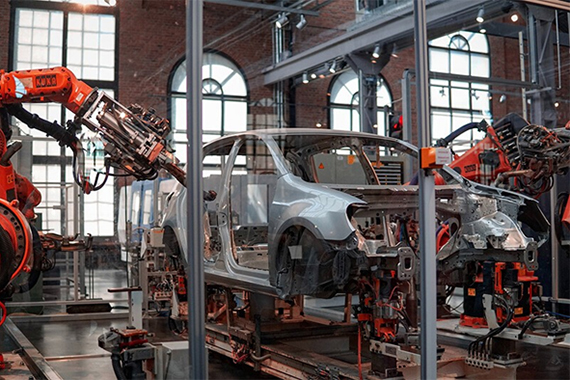
Research Revelations
What will factories look like in the post-pandemic era?
Manufacturing will look strikingly different in the post-pandemic era, says a Purdue University expert in supply chain and manufacturing management.
“But we’re really bullish on the future of manufacturing,” says Ananth Iyer, senior associate dean in the Krannert School of Management and director of the Dauch Center for the Management of Manufacturing Enterprises (DCMME). “We want manufacturers everywhere to come out swinging because that’s the only way the supply chain will ramp back up. And we actually think that, however bad the pandemic gets, there is a bright future.”
Iyer is the lead author of a recent working paper that lays out a framework for recovery based on surveys of senior management personnel at about 50 manufacturers in Indiana. Coauthors include Steve Dunlop, DCMME’s managing director, as well as Angus McLeod and Roy Vasher, who are both affiliated with the center.
Results from the survey show that rigorous infection control, social distancing enforcement and technology expansion will be the new normal for manufacturers that are managing through the pandemic, weathering shutdowns and restarting operations.
Many manufacturers are now considering COVID-19 as they map out their operations to optimize labor processes and the flow of materials, a practice called value stream mapping. By including the virus in this thought process, producers say, they are mitigating the chance of their workers becoming infected.
“Without a good map of your processes, where the workstations are, and what people are doing, you really don’t have a good way to systematically understand what the health risks are for this infection,” Vasher says. “You have to know how many people are standing within six feet, how many people are touching a surface and how many people are handling the same tools. Without understanding these risks, then you don’t know what mitigation to apply.”
To address health risks, manufacturers are requiring employees to wear gloves, cleaning and disinfecting tools, and spacing workstations six feet apart by outlining squares or circles on factory floors. They also are adjusting the number of employees per shift, increasing the number of shifts per day, and staggering the start time of shifts to eliminate the chance of workers coming into close contact with each other.
Instituting these infection control and social distancing measures will increase labor costs, as companies will have to track their workers more closely, run smaller shifts and ramp up their cleaning protocols. This will lower the threshold for businesses to adopt new technologies that ease these processes and increase production.
“Given that is the case, it is absolutely the right time to think about adopting technology because what was not justifiable before becomes justifiable now,” Iyer says. “Technology providers will further decrease costs with increased adoption, so even smaller companies should really be thinking about this.”
Ford, for example, is testing wristbands that sense and alert workers when they are within six feet of someone else. And there are likely more innovations on the horizon, Iyer adds.
“These days, for counting and checking inventory, drones have become common. Co-bots can help complete tasks that require two people, and cleaning robots are becoming commonplace for manufacturers,” he says. “Fast adoption of lots of new technologies could be the way that companies can both protect their employees while continuing to produce and adhere to their new processes.”